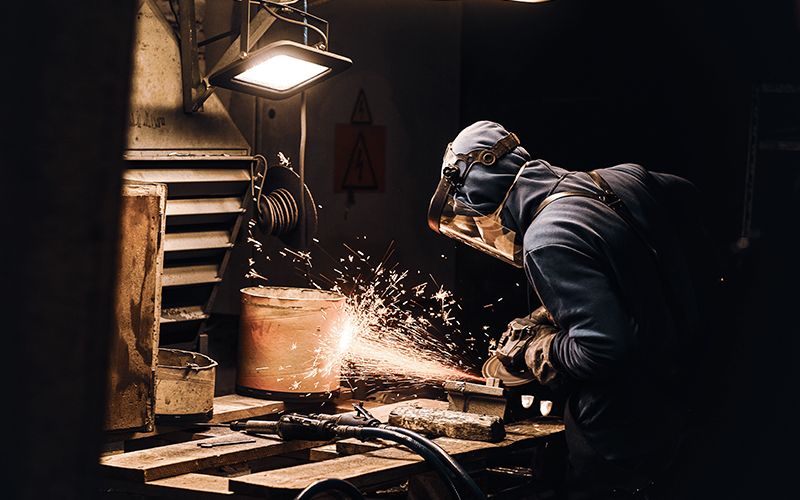
¿Qué diferencia hay entre la soldadura MIG / MAG y TIG? ¡Te lo contamos aquí!
¿Qué diferencia hay entre la soldadura MIG / MAG y TIG? ¡Te lo contamos aquí!
La soldadura MIG y TIG son dos técnicas populares utilizadas para unir metal. Ambas técnicas ofrecen soluciones de soldadura de alta calidad, pero cada una tiene sus propias fortalezas y debilidades que deben ser consideradas al elegir la técnica adecuada para un proyecto específico.
¿Qué diferencia hay entre soldadura MIG y TIG?
La soldadura MIG MAG, es una técnica de soldadura en la que utiliza un electrodo de metal que se alimenta continuamente a través de un hilo. La soldadura MIG MAG es ideal para proyectos de gran escala debido a su rapidez y eficiencia, y es adecuada para una amplia variedad de materiales, incluido el acero inoxidable, el aluminio y el cobre.
Por otro lado, la soldadura TIG, también conocida como soldadura por arco de tingsteno, es una técnica de soldadura por arco que utiliza un electrodo de tungsteno no consumible y un gas de protección inerte para proteger el baño de la soldadura. La soldadura TIG ofrece un control preciso y una calidad de soldadura uniforme, lo que la hace ideal para proyectos de precisión y aplicaciones críticas. Sin embargo, la soldadura TIG es un proceso más lento y requiere habilidades manuales especializadas, lo que la hace más adecuada para proyectos más pequeños y de menor escala.
En términos de costes y calidad, ¿qué diferencia hay entre soldadura MIG MAG y TIG?
En términos de costo, la soldadura MIG/MAG es generalmente más asequible que la soldadura TIG debido a la menor cantidad de equipo y materiales requeridos. La soldadura MIG MAG también requiere menos habilidades manuales, lo que la hace más adecuada para principiantes o trabajadores menos experimentados.
En términos de calidad de soldadura, la soldadura TIG ofrece una calidad de soldadura uniforme y un control preciso, lo que la hace ideal para proyectos críticos y de alta precisión. Por otro lado, la soldadura MIG MAG ofrece una rapidez y eficiencia superiores, lo que la hace ideal para proyectos de gran escala.
En conclusión, la elección entre soldadura MIG y TIG dependerá de las necesidades específicas de cada proyecto. La soldadura MIG es ideal para proyectos de gran escala y para principiantes, mientras que la soldadura TIG es adecuada para proyectos de precisión y críticos. Cualquiera de estas técnicas puede ofrecer soluciones de soldadura de alta calidad, pero es importante tener claro desde el principio qué clase de proyecto vamos a abordar. Puedes contactar con nosotros para cualquier consulta que desees resolver.